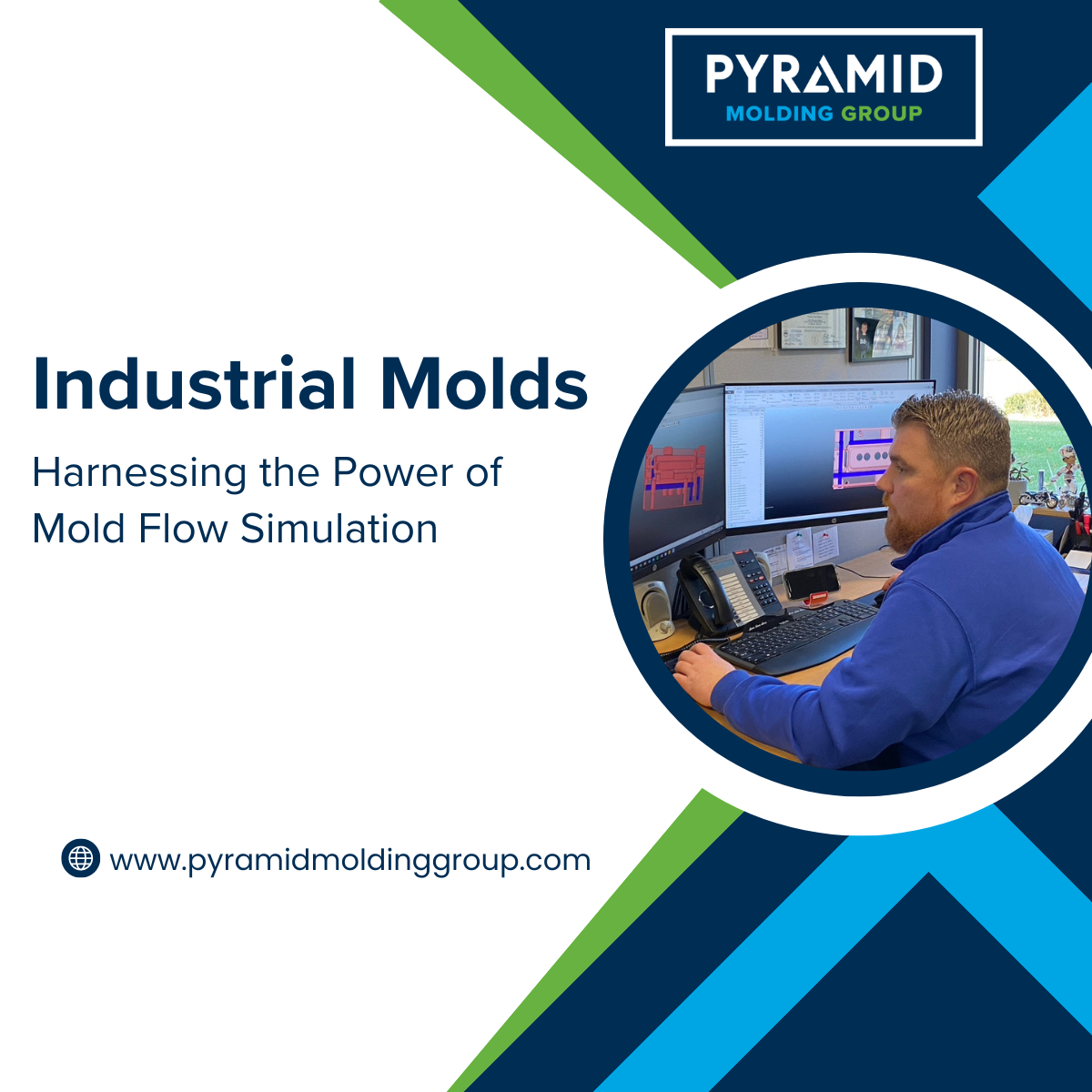
In today’s fast-paced manufacturing world, efficiency, accuracy, and cost-effectiveness are paramount. By harnessing the power of mold flow simulation, we can optimize the entire plastic injection tool-building process, leading to superior results and substantial benefits. Here’s why utilizing mold flow software is a must:
Precision at Every Stage: Mold flow software empowers engineers and designers to analyze and visualize the behavior of molten plastic during the injection molding process. By simulating the flow, cooling, and solidification of plastic, we can identify potential defects, such as warpage, sink marks, or air traps, even before the tooling process begins. This level of precision enables us to fine-tune designs, select optimal materials, and optimize cycle times, saving both time and money.
Design Optimization: With mold flow software, we can simulate various design iterations and evaluate their performance under different molding conditions. By analyzing factors like gate location, runner design, and part thickness, we can identify the most suitable design that maximizes part quality and minimizes production challenges. This iterative process allows us to avoid costly trial-and-error methods and fine-tune designs for optimal performance.
Cost Reduction: The ability to foresee potential defects and optimize the design translates into substantial cost savings. By identifying issues early in the process, we can avoid costly tool modifications, production delays, and scrap rates. Mold flow software helps us optimize gating and cooling systems, reduce cycle times, and minimize material waste, ultimately enhancing productivity and profitability.
Collaborative Advantage: In a highly collaborative industry, mold flow software fosters effective communication among design engineers, toolmakers, and injection molders. By sharing simulation results, we can have constructive discussions, gain valuable insights, and make informed decisions collectively. This synergy enhances overall efficiency and ensures that everyone involved is aligned toward achieving optimal results.
Embracing mold flow software in plastic injection tool building is not just a choice; it’s a necessity for staying ahead in today’s competitive market. By leveraging the power of simulation, we can optimize designs, reduce costs, enhance quality, and foster collaboration, all while delivering exceptional value to our customers.
Industrial Molds has embraced this transformative technology and unlocked new frontiers in plastic injection tool building! Let’s revolutionize the industry and shape a brighter future!
Recent News
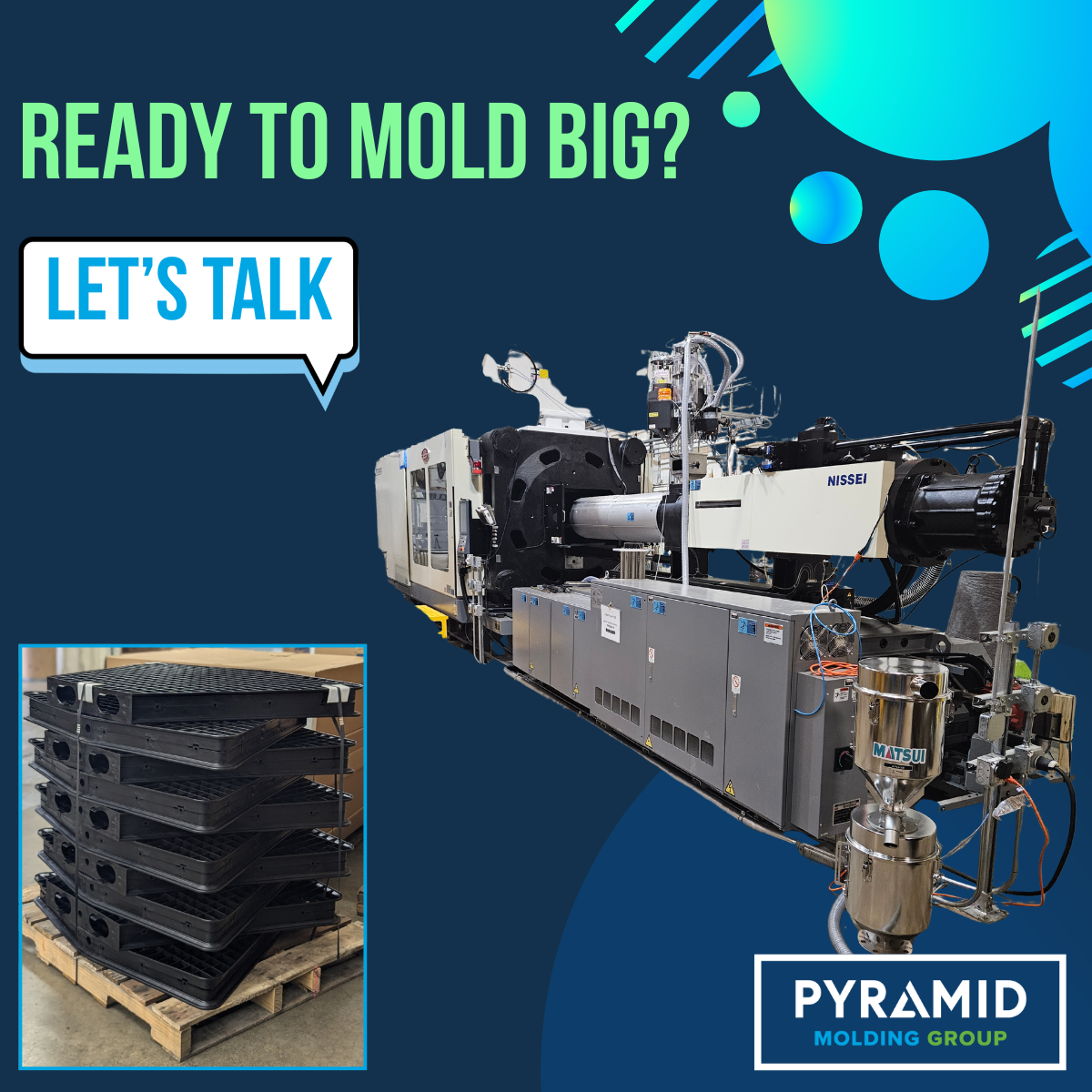
Large Part Molding in the USA: Why Our 1,000-Ton Injection Molding Press Sets Us Apart

Remove Supply Chain Uncertainty
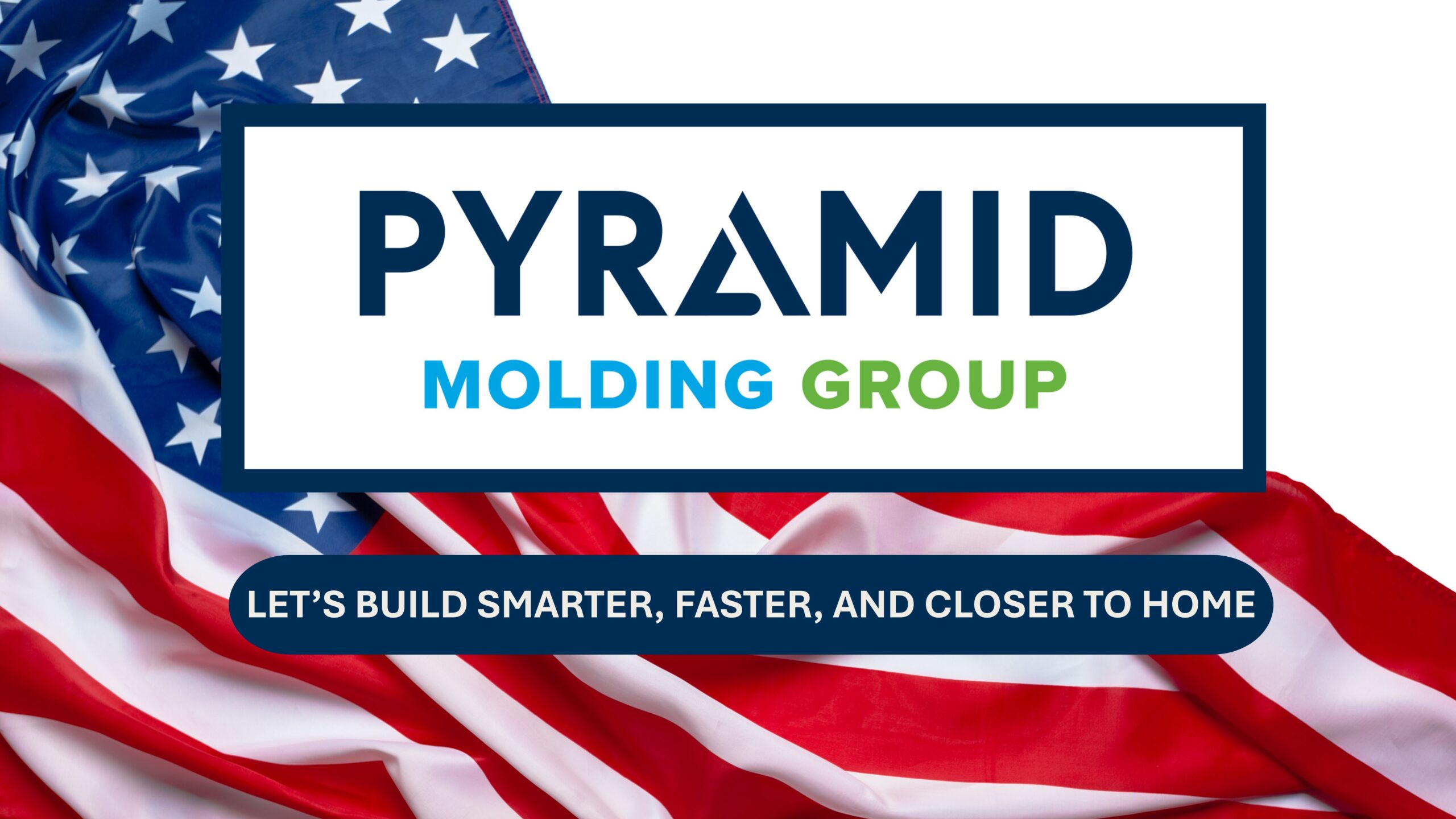
Seamless Support, Reliable Manufacturing: The Value of a U.S.-Based Partner
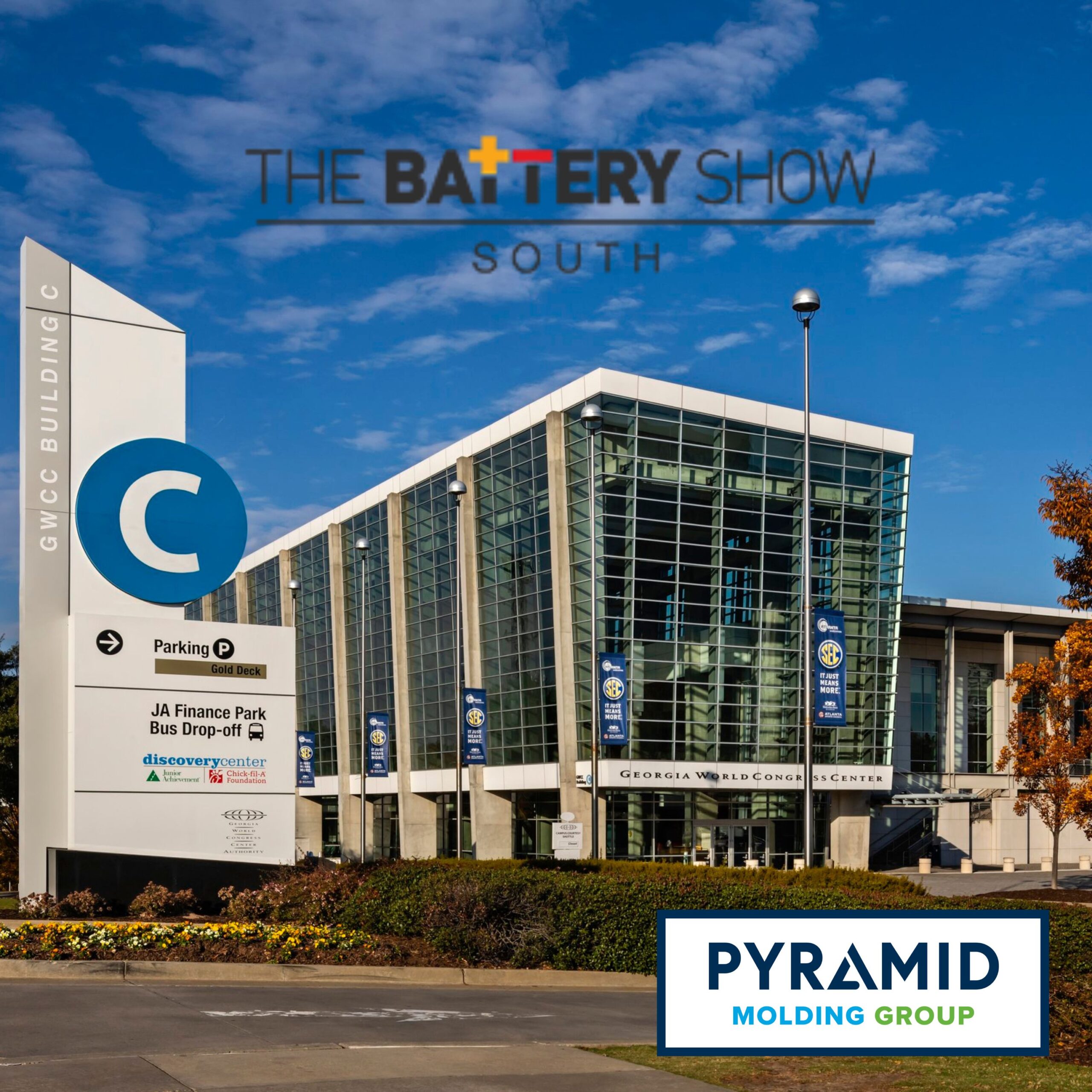
PMG Takes on Atlanta at the Georgia World Congress Center!
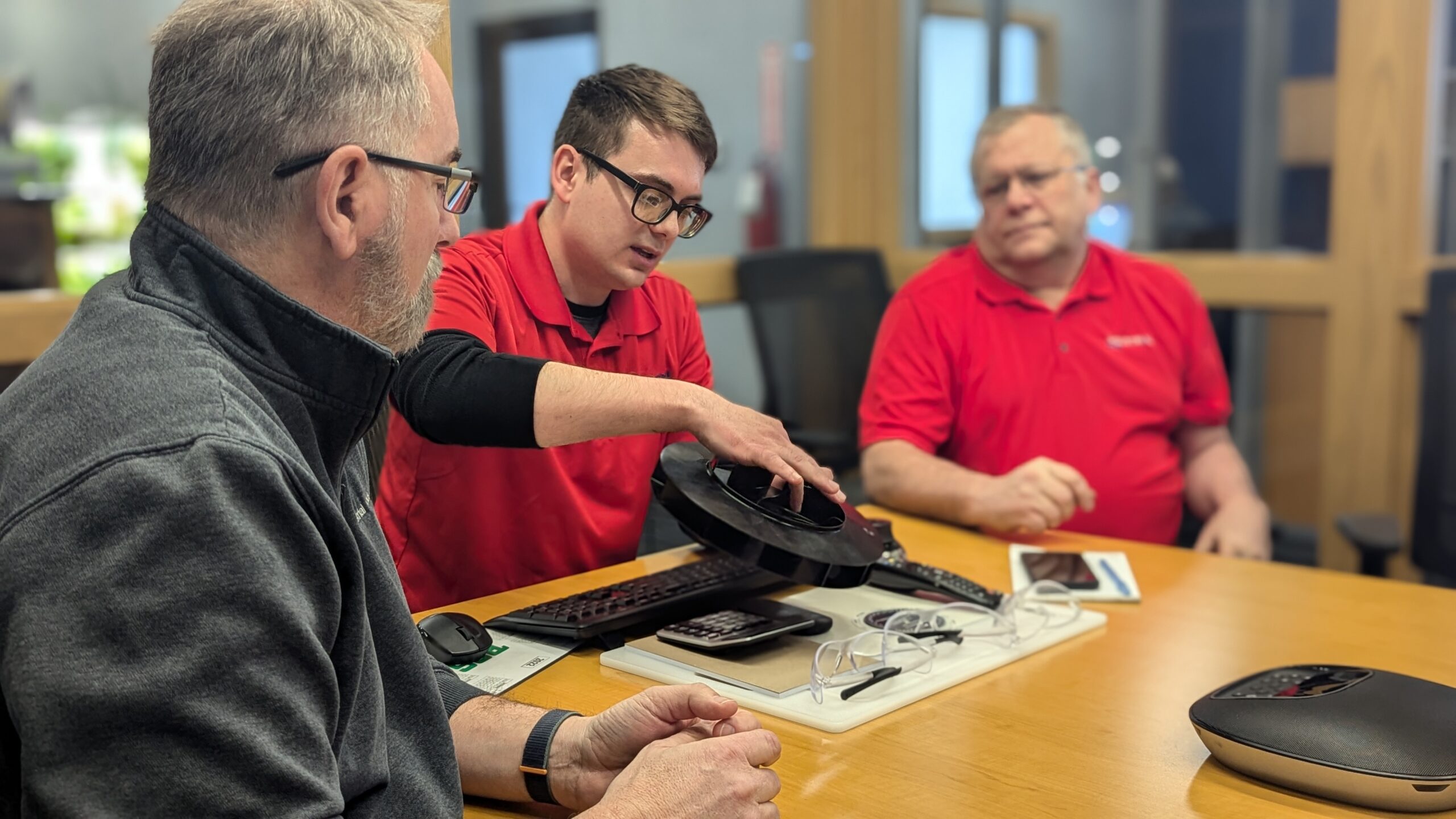